Stress Corrosion Cracking on French NPPs – an overview
- Jan Bartak and Noël Camarcat
- Dec 11, 2023
- 15 min read

Abstract:
The paper provides an overview of the stress corrosion cracking phenomena first detected on certain reactors of the French nuclear fleet in October 2021, in the middle of the European energy crisis, reducing the availability of the French nuclear fleet to historically low levels.
After a short presentation of the different reactor types in the French fleet, the paper describes the stress corrosion cracking phenomenon and its unexpected presence in the vicinity of welds on the elbows of safety injection systems and/or residual heat removal systems of certain reactor types. We further describe the history of the progressive discovery of the defects by EDF and the unprecedented repair strategy and research programme aiming to understand the phenomenon and its causes, to develop adequate detection methods and implement them across the fleet while maintaining aggressive objectives to reconnect the reactors to the grid, strictly respecting nuclear safety requirements and cooperating closely with the regulator. The future preventive maintenance strategy for the detection, mitigation and repair of the stress corrosion cracking defects and the main lessons learned from this unique experience are summarised. Less than two years after the detection of the first defect, EDF seems to have mastered the treatment of the problem in a very short timeframe.
1. Introduction – the French nuclear fleet
The French nuclear fleet is well known for the high level of standardisation of its reactors. The fleet, built essentially over less than three decades starting from 1971 and until the end of the last century (Figure 1), is composed of three main types of reactors: the first series of thirty-two reactors were of the CP type. These are 900 MW 3-loop reactors, with three sub-types: CP0, CP1 and CP2 (the latter two typically referred to jointly as CPY). The 900 MW reactors were followed by a batch of twenty 1300 MW 4-loop reactors with two subtypes: P4 (8 reactors at 3 sites) and P’4 (12 reactors at 5 sites), and finally by the most recent four N4 type 4-loop reactors, 1450 MW. Altogether, after the shutdown of two 900 MW reactors at Fessenheim in 2020, there are currently 56 operating power reactors in France, distributed over the territory of the country as indicated in Figure 2.

Fig. 1: The schedule of construction of the French reactor fleet
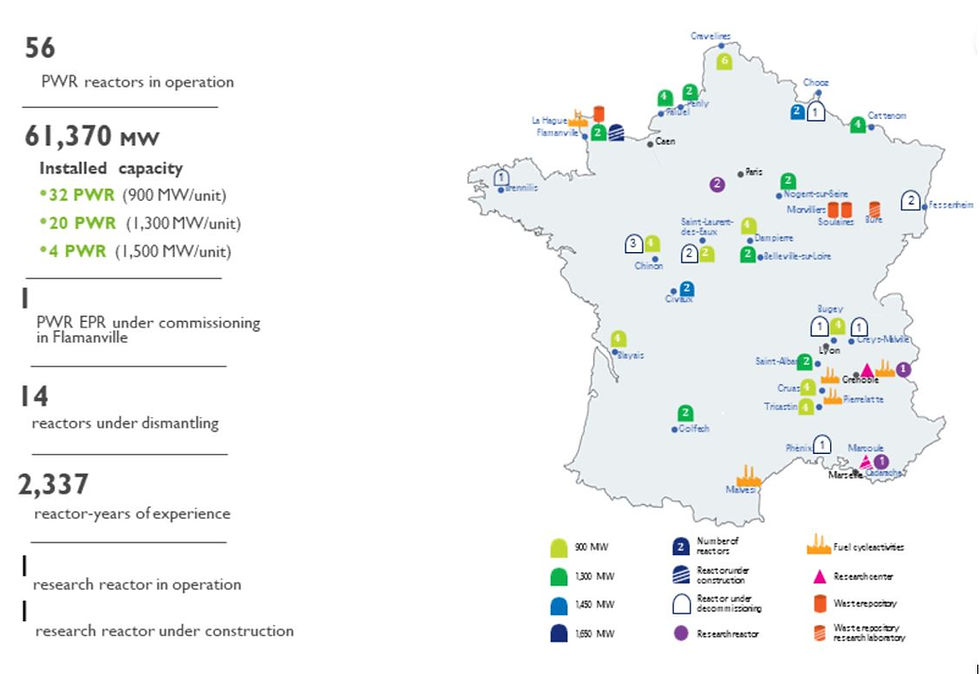
Fig. 2: The French nuclear fleet (courtesy I2EN)
2. Unexpected and previously unknown type of stress corrosion cracking
The recently observed stress corrosion cracking phenomenon was totally unexpected and caught the operator, EDF, by surprise. It occurred at the peak of the 2022 European energy crisis where nuclear power had a unique opportunity to demonstrate its resilience to the disruption of supply of imported fossil fuels, on which the electricity sector of the continent was excessively dependent, revealing a total lack of concern about Europe’s energy security. Unfortunately, due to the unexpected occurrence of these defects, nuclear power failed in demonstrating such resilience, an argument immediately exploited by anti-nuclear activists and organisations. However, the true reasons are more political than technical. The industry and the regulator were fully aware of the risk of a generic failure occurring on a fleet of standardized reactors and repeatedly warned the politically authorities that the only way to hedge against this risk is to have sufficient margin in the system, to have both nuclear and non-nuclear dispatchable reserve sources capable to support the possible loss of several reactors due to a generic defect of failure. Despite this, the government decided to shut down 11 GW of dispatchable fossil plants and 1.8 GW of nuclear generation based on purely political or ideological considerations.
Safety is always the first imperative of nuclear operators, detecting a defect with potentially serious consequences inevitably resulted in the shutdown of a large number of reactors, this coming on top of long-term ten-yearly outages carried out on multiple reactors and certain delayed outages due to the COVID 19 pandemic. As a result, in summer 2022, 32 reactors (out of 56) were off-line when the gas prices were peaking at 350 €/MWh. EDF’s generation dropped to 279 TWh in 2022, the lowest level since 1992, compared to 361 TWh in 2021.
Surprisingly, the detected stress corrosion phenomenon occurred only on certain types of reactors, specifically those of the N4 and P’4 types, while others, mainly the oldest CP type, have shown to be much less sensitive to the phenomenon. Even with thousands of reactor-years of cumulative global operational experience, new unexpected phenomena still can occur and present new challenges to the nuclear industry.
The detected defects can be characterised as being (1) serious, (2) unexpected and hitherto unseen on the global light water reactor fleet, and consequently with no or very limited experience feedback, (3) difficult to detect with traditional non-destructive methods (the “signature” of these defects is quite different from the well-known thermal fatigue phenomenon) and, last but not least, (4) difficult to repair, since the defects were located in the immediate vicinity of the reactor, where radiation levels impose constraints on the duration of workers’ presence to keep the absorbed radiation dose within regulatory limits.
3. The phenomenon of stress corrosion cracking
Stress Corrosion Cracking (SCC) is a well-known phenomenon in the nuclear industry. It concerns austenitic stainless steels that compose almost exclusively the primary coolant systems of light water reactors. The SCC phenomenon occurs under the effect of three concomitant factors:
· sensitive material,
· favourable chemical medium and
· tensile stresses in the material.
This corrosion phenomenon is therefore a multiparameter mechanism, which complicates the investigation of the conditions of its appearance. EDF specialized teams detailed the occurrence of the above factors in the context of the French nuclear fleet at a dedicated SFEN[1] conference in Paris on March 29, 2023.
The first factor is the sensitivity of the material to stress corrosion. In the case of a PWR primary circuit, the material is a traditional austenitic stainless steel, commonly used in industry for its good corrosion resistance and is not known to be sensitive to SCC in pure primary PWR medium unless the material is hardened. Stress hardening is a deformation of the material during the various stages of manufacture which has the effect of increasing its hardness and sensitivity to the phenomenon of stress corrosion. To avoid this hardening, a high-temperature heat treatment is carried out at the end of the manufacturing process to restore the properties of the material. But post-fabrication operations and in particular the welding of portions of pipes together on site can induce deformations of the material near the welded area.
Regarding the second factor, chemistry, extensive experience is available across the nuclear industry showing that the presence of pollutants in the water, in particular chlorides, induces the appearance of SCC. The phenomenon has been observed either in auxiliary circuits where such pollutants can be present or in cases of accidental pollution of circuits containing pure water. On PWR primary circuits and circuits connected to them about 150 cases have been identified worldwide in the last thirty years. Reactors of all ages have been affected and the origins of the cases are very diverse.
On the primary circuit of French PWR fleet, where the water quality is scrupulously controlled and monitored (pH, oxygen levels, pollutants, etc.), extensive data are available covering the past operational life for all reactors. To date, no anomaly was detected that could explain a significant increase in the risk of SCC in the reactors concerned. Compliance to chemical specifications has been particularly stressed by EDF at the SFEN conference. The absence of pollutants presents a significant difference with the previously known SCC cases on auxiliary circuits. Cracking of stainless steel in nominal environments, although identified as a potential risk in the PWR community, remains rare across the global nuclear industry.
The third factor of SCC, stresses in the material, on the other hand, can be generated by welding (residual stresses), by the erection of piping and by their operating conditions (pressure and temperature). The design and the layout of the piping can also play a role as the stresses vary and change their distribution along the piping with temperature changes.

Fig. 3 The three factors underlying the Stress Corrosion Cracking phenomenon
The underlying physics-chemical mechanism of SCC is presumably thermally activated oxidation. This implies that for a given configuration of the three source factors described above, the cracks will occur earlier and propagate faster at higher temperatures. Consequently, the phenomenon can be detected only after it actually occurs, which can be several decades after the installation of the piping. The propagation velocities of the observed stress corrosion cracks are variable, of the order of magnitude of a millimetre per year. The characteristic pattern of the cracks (unlike thermal fatigue cracks) is that they follow the grains of the material (see Figure 4).

Fig. 4: Stress corrosion cracks in stainless stell in contact with primary fluid
4. The history of detection of SCC on the French nuclear fleet, limitations of existing non-destructive methods
In October 2021, following ultrasonic checks scheduled during the second ten-yearly outage of the Civaux NPP reactor N°1[2], EDF detected signals revealing the possible presence of a defect on welds on the elbows of the safety injection system (RIS). As a precaution, the Civaux NPP reactor 2 was also shut down. Subsequent checks confirmed the presence of indications similar to those of reactor 1. The suspected parts of the piping were removed. Metallurgical analyses conducted on these parts of the pipes revealed the presence of cracking resulting from an unexpected stress corrosion phenomenon on the inner surface of the piping, close to the weld bead. It should be noted that the defects occurred in the portion of the piping immediately adjacent to the primary circuit piping, downstream of the RIS isolation valves. This implies that should a leak occur at this location; it could not be isolated.
The non-destructive ultrasound checks carried out during the ten-yearly outages aim to detect the presence of cracking by thermal fatigue. The method is far less effective at detecting stress corrosion cracking. When certain signals not corresponding to the typical “signature” of thermal fatigue were detected in the past, they may have been classified as spurious.
Through verification of the historic test recordings, it was quickly revealed that indeed similar signals were classified as spurious during the recent ten-yearly outages on the other two N4 reactors (Chooz B NPP reactors 1 and 2). Respecting the “safety first” principle, EDF shut them down in order to carry out additional checks.
At the same time, the Penly NPP reactor N° 1 (1300 MW – P’4 type) was undergoing its third ten-yearly outage. Similar defects were observed on the same pipes. Laboratory analysis of the removed parts also concluded that stress corrosion cracking was present, even though at a smaller scale than on the Civaux 1 reactor. This implied that the defect was not specific to one type of reactor but could be generic.
EDF rapidly developed a control strategy that was validated by ASN, the French safety authority. This strategy covered all types of reactors in the fleet and required carrying out pipe cuts on a representative sample of reactors, metallurgical expertise after cutting being at this stage the only way to decide, with certainty, on the presence of SCC defects. A reference reactor was chosen for each reactor type existing within the fleet. For the reference reactor, all past recordings of non-destructive ultrasound controls were re-checked to reveal similar recording patterns previously classified as spurious. As a result of this analysis, seven additional reactors were shut down in addition to the original five (two at Civaux, two at Chooz B and one at Penly). EDF concluded that there was no other alternative to cutting the portions of pipe with the identified cracks and carrying out detailed laboratory analyses. In all, 115 welds have undergone expertise, 230 samples were studied using powerful microscopes in EDF’s specialised material expertise laboratory LIDEC near Chinon in France, unique in Europe.
In parallel, EDF established a 15-member high-profile international expert team to progress in the understanding of the phenomenon. The team confirmed EDF’s conclusions and recommended to study further the temperature distributions in the circuits and the concentration of oxygen in the fluid.
Preliminary conclusions were drawn and later confirmed as the number of analysed defects increased that the determining factor with regard to the sensitivity to SCC defects was not the age of the reactors but the geometry and thermalhydraulic conditions of the circuit piping, specifically thermal stratification – a separation of warmer and cooler flows within the lines, which led to high stresses in the U-shaped piping resulting in SCC in pipe elbows adjacent to welds. The relatively complex geometry of the safety injection system (RIS) piping in type P’4 modification of the 1300 MW reactors and of the 1450 N4 reactors was the most prone to the development of the SCC defects. EDF proposed a classification of the sensitivity of auxiliary piping of the reactors of the fleet to the SCC phenomenon and concluded that in particular the RIS lines connected to the cold leg of the primary loop and the residual heat removal system (RRA) lines connected to the hot leg of the primary loop of type N4 reactors and the safety injection system (RIS) lines connected to the cold leg of the primary loop of type P'4 reactors as being the most sensitive to the phenomenon of SCC. On the other hand, the CP-type reactors (900 MW – 20 in the fleet) and type P4 reactors (1300 MW – 8 in the fleet) have shown limited or no sensitivity to the SCC defects due to the different geometry of the RIS and RRA lines. These findings are summarised in Table 1 below.

Table 1: The systems and portions of their piping that were found sensitive to SCC on the reactors of the French fleet
The RIS and RRA circuits are presented in Figure 5 and the layout of the RIS piping with the welds in the proximity of which the SCC defects were observed is presented in Figure 6.
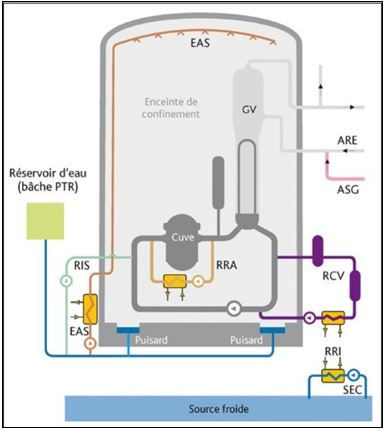
Fig. 5 The safety injection system (RIS) and residual heat removal system (RRA) in the French PWR

Fig. 6 Geometry of the safety injection system (RIS) piping and its connection to the primary circuit
Altogether, portions of the RIS lines were cut off and replaced on 10 reactors. This repair and replacement program represented a major maintenance operation mobilising multiple experienced nuclear industry companies and hundreds of qualified workers and welders, a number of them from USA (Westinghouse). The operations were carried out in a complex and constrained environment in immediate proximity of the reactor and had to be managed rigorously to minimise the integral dose absorbed by the workers. The repair works were carried out throughout the year 2022 to ensure the availability of the reactors for electricity supply in a particularly challenging winter 2022-2023 in the context of the energy crisis in Europe.
To enhance its capacity to detect and measure SCC on stainless steel piping and avoid the need of cutting off the pipes to determine the presence of SCC defects, EDF undertook significant R&D efforts to develop an improved ultrasound control method that allows to detect even very small cracks and measure their depth with sufficient precision. This tool was developed in record time and was validated by the international expert team and approved by ASN. Using this tool, EDF prepared a vast industrial program of checks on all reactors of the fleet in the coming years.
5. New SCC suspect – welds repaired during plant construction
The systematic testing of reactors in the fleet with improved methods was bound to identify new issues. This has been often the case in the nuclear industry as new technology allows improved detection methods to be deployed.
In March 2023, a different type of the SCC phenomenon was revealed on the French fleet.
A crack was detected in the proximity of a weld on the safety injection system (RIS) connected to the hot leg of the primary circuit of reactor 1 at the Penly NPP. The crack extends 155 mm, or about a quarter of the circumference of the piping, and its maximum depth is 23 mm, for a pipe thickness of 27 mm. As opposed to previously identified SCC cases, this line was considered not to be susceptible to SCC due to its geometry. However, this weld was the subject of a double repair during the construction of the reactor, the first to correct misalignment of pipe sections, the second to correct a welding effect. This double repair was likely to modify the mechanical properties and the internal stresses of the metal in the vicinity of the weld. The case was classified by ASN as a level 2 event on the INES scale, since in the presence of such a crack the resistance of the piping can no longer be demonstrated. However, the reactor safety demonstration takes into account the rupture of one of the safety injection lines. There are three redundant safety injection systems, so there is no risk of core melt in the case of a pipe break on one of them. In its safety analysis, EDF has shown that 2 RIS injection lines are sufficient on a 1300 MW reactor to avoid core melt.
Roughly at the same time, thermal fatigue cracks on lines considered sensitive to stress corrosion phenomena of the safety injection circuit (RIS) were detected on reactor 2 of the Penly NPP and reactor 3 of the Cattenom NPP, both P’4-type reactors. The pipes concerned were replaced as part of EDF's program on the RIS lines of P'4-type reactors. These events were classified at level 1 of the INES scale by ASN.
Since the detection of SCC in the proximity of welds that were repaired during the construction of the plant, EDF had to revise and extend the overall control and testing strategy and implementation program: all welds that had undergone repair during the construction of the reactors in the French fleet were included in the test program. This new program was validated by ASN in April 2023.
6. EDF future control and repair strategy and its implementation
The revised and enhanced control and repair strategy redefined the priorities of the work to be done.
320 welds of the RIS and RRA lines across the fleet were identified as having undergone repairs at the time of reactor construction. Sixty-nine of these were judged to be the most sensitive to SCC (in particular those repaired twice) and will be treated with the highest priority. The revised strategy targets to check more than 90% of this priority group of repaired welds by the end of 2023, the remaining ones will be checked by the end of first quarter of 2024. EDF has also put in place additional operating measures to prevent operating situations that would cause significant stress on these welds, as well as measures to quickly detect any leaks. These operating measures will be implemented until the next scheduled shutdowns of reactor 1 of the Nogent-sur-Seine NPP (P’4-type 1300 MW)) and reactor 2 of the Cruas NPP (CP2-type 900 MW), scheduled for September 2023. The originally repaired welds on these two reactors were evaluated as having the highest priority for their control.
All the reactors of the fleet, including all P4-type and CP-type reactors will undergo testing for SCC on all systems using austenitic steel lines with repaired welds using the newly developed non-destructive methods and tools before the end of 2025.
The work is planned to minimise the impact on generation, taking benefit from refuelling or other planned outages, while nuclear safety remains the overarching priority.
It should be noted that SCC in the proximity of repaired welds was observed on certain reactors in the global fleet. In some countries, the USA in particular, the technology of weld overlays has been qualified by the regulators to protect the piping without the need to replace it. A study caried out in 2012 by the Pacific Northwest Nuclear Laboratory in the US concludes that “weld overlays provide effective mitigation against the initiation of primary water SCC and against the growth of existing SCC allowed by the design to remain in service[3]“. It remains to be seen if this approach could be qualified in France.
7. Lessons learnt and future work
The key lessons learnt from this new type of SCC have been summarised by the chairman of the French regulator, ASN, during a parliamentary hearing in October 2022.
The first lessons learnt is the necessity of prudence and modesty: our knowledge and understanding is never complete, it evolves permanently, new and unexpected phenomena are to be expected. There is a need to constantly improve non-destructive control methods and be ready for the unexpected, have sufficient highly specialised industrial and human capabilities to deal with similar situations.
The second lesson learnt is that operators should develop the capability to search for the unexpected, improve their preventive maintenance plans and procedures, look for defects in places which are not routinely controlled. In this respect the discovery of these unexpected SCC phenomena demonstrates the usefulness of obligatory periodic in-depth inspections as practiced on the French reactor fleet. The observed SCC had gone unnoticed in the previous decennial inspections (assuming they were already present) because the non-destructive inspection techniques were not adapted or not sufficiently performant to detect this type of SCC. The focus for the fleet decennial visits after 2010 was more on thermal fatigue detection than on stress corrosion cracking, supposedly unlikely to happen on austenitic steels in those operating conditions.
The third lesson learnt, not a new one though, that with a large portion of nuclear reactors in the energy mix, a sufficient safety generation margin must be maintained, in proportion to the size of the fleet, in order to allow simultaneous shutdown of several reactors in case of a generic defect, failure or anomaly.
8. Conclusions
In October 2021, following ultrasonic checks scheduled during the second decennial outage of the Civaux NPP 1450 MWe reactor N°1, and shortly thereafter on other reactors of the N4-type (1450 MWe) and the P’4-type (1300 MWe), EDF discovered previously unseen on the global nuclear fleet stress corrosion cracks on the safety injection and residual heat removal systems in immediate vicinity of the reactor vessel, resulting in long-term shutdown of a dozen of reactors. In conjunction with ongoing decennial outages on multiple reactors and certain delayed outages due to the COVID 19 pandemic, a total number of 32 reactors were unavailable in summer 2022.
EDF has undertaken a massive strategy of preventive replacement of the pipe sections identified as sensitive, while at the same time deploying an unprecedented programme to develop the understanding of the causes, to develop enhanced detection methods and future preventive maintenance programmes, all in close coordination with the regulator, while maintaining the objective of having most of the reactors back on-line before winter 2022-2023.
Almost two years after the discovery of the first defect, EDF has mastered the treatment of the problem and is confident about the implemented fixes and future detection methods, this confidence being supported by positive, though necessarily cautious, opinions of the regulator. By the middle of May 2023, all the incriminated piping on the N4 and P’4 reactors was repaired and the reactors back on-line.
The exemplary treatment of this unexpected problem echoes the words of Georges Lamiral, author of a well-known book describing the glorious era of the French nuclear development 1960-1990: “It happens to the French to make mistakes and to face failures, but one of their main qualities is to know how to react quickly”.
References
[1] SFEN: French Nuclear Energy Society (Société Française d’Enérgie Nucléaire)
[2] Civaux 1 is one of the 4 reactors of the N4 type, nominal power 1450 MWe
[3] EJ Sullivan, MT Anderson: Assessment of Weld Overlays for Mitigating Primary Water Stress Corrosion Cracking at Nickel Alloy Butt Welds in Piping Systems Approved for Leak-Before-Break, PNNL-21660, 2012
[4] Public hearing relative to the problems of stress corrosion cracking encountered on the EDF nuclear fleet, 27 October 2022 – Parliamentary Office for the Evaluation of Scientific and Technical Options (https://www.assemblee-nationale.fr/dyn/16/comptes-rendus/ots/l16ots2223154_compte-rendu) [5] SFEN conference on the stress corrosion cracking phenomena observed on the French nuclear fleet, 29 March 2023
Comments